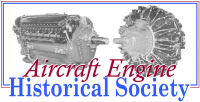 |
enginehistory.org Aircraft Engine Historical Society Members' Bulletin Board
|
View previous topic :: View next topic |
Author |
Message |
dpennings
Joined: 10 Dec 2016 Posts: 48
|
Posted: Sun Nov 29, 2020 03:45 Post subject: |
|
|
the discussions here can last decades...
V12 engines for Diesel locomotives can have a TBO of 20.000 h plus, it is not depending on crank case stiffness. Radial engines had lower rpm because of the extremly heavy masses acting on the single crank, that lowerd wear on the cylinders and valve train components whereas V12 engines could rev higher. You could as well build a V12 engines for low rpm, but than the power to weight ratio will be much worse than for the radials.
Somewhere I read, that about 50 % of all engine failures of liquid cooled engines came from leakage of the cooling system, that was one important reason not to choose them for civil aviation. |
|
Back to top |
|
 |
rwahlgren
Joined: 15 Aug 2003 Posts: 323
|
Posted: Sun Nov 29, 2020 23:05 Post subject: |
|
|
Diesel locomotive engines ? Different application than an aircraft engine
V12 EMD Engine weights 28,000 lbs, and yes sir the block / crank case is many orders of magnitude, stronger and much stiffer than any cast aluminum inline V12 aircraft engine, the weight alone tells you that.
The same EMD 645 V12 is rated at 2300 HP, at 900 RPM, and displaces
7,740 Cubic Inches.
Crankcase strength is most important for longevity. Yes most aircraft V12 inlines use the cylinder bank assemblys for added strength, even that is not going to come close the the EMD Locomotive engine. |
|
Back to top |
|
 |
dpennings
Joined: 10 Dec 2016 Posts: 48
|
Posted: Wed Dec 09, 2020 14:48 Post subject: |
|
|
there are incredible many inline engine out there, even aluminum crank cases for Diesel engines, most of them will last a very long time and there is no typical engine failure due to week crankcase stiffness. Can you give mention one common failure mode because of a lack of engine stiffness?
Low crank case stiffness will contribute to higher noise levels, that's why you will find a lot of stiffening rips on crank cases, but this has little to do with engine life expectations. The only two applications which really depend on high crank case strength are tractor and race engines, where the crank case is part of chassis.
On the other hand I don't know a single high revving radial engine, no matter how strong the crank case might be, seems like it has little to do with that. Despite that, the crank case might be strong, but separated cylinders (typical for most air cooled engines, even in inline configurations) tend to bend significantly by the side forces of the piston, water cooled inline engines provide much more stiffness to the cylinders.
Air cooled radial engines offered reliability because of not having a potential leaking cooling system and a high life expectation because of lower specific power and engine speed. Despite the lower specific power output, the engines had no weight penalty because of the very short and light crank shaft/crank case. The separated cylinders allowed easy maintenance and replacements of parts, another big advantage.
V12 engines had nearly always reduction gears whereas radial engines were better suited for direct drive. I know, the very large and highly developed radials had reduction drives, unlike the radial, thy used coaxial planetary gears which saved weight compared to the stern drives of the inline engines. Later ones needs stern drives to move the propeller shaft upwards.
The air cooled radialsengines offered reliability because of not having a potential leaking cooling system and a high life expectation because of lower specific power and engine speed. Despite the lower specific power output, the engines had no weight penalty because of the very short and light crank shaft/crank case. The separated cylinders allowed easy maintenance and replacements of parts, another big advantage. |
|
Back to top |
|
 |
rwahlgren
Joined: 15 Aug 2003 Posts: 323
|
Posted: Thu Dec 10, 2020 21:57 Post subject: |
|
|
Maybe Kim could answer the above?
"Engine stiffness"? Or Crankcase?
The one common failure mode is main bearing distress or failures.
Another is cracking and complete crankcase/ block failure.
Just watch some tractor and truck pulls where the forces pull the integral cylinder block off its cast iron crankcase, leaving the pistons and rods to flap in the air.
If the crankcase is a wet noodle it can not support the distortions caused by firing pressures, and mounting and torque loads, thus allowing distortion that can cause crankshaft misalignment with in the line bored bearing bores, and distortions that over stress certain area's causing cracking .
Engineers of the past, put much thought and testing into the block-crankcase design, using stress coat and strain gauging. It is the main foundation of the engine, and is very very important. You wouldn't want your house sitting on substandard concrete.
The aluminum castings for inline engines like the Allisons, and Merlins have to be reinforced or redesigned for very high HP or Torque outputs, that is if they are expected to last very long.
Crankcase stress must be important enough to spend untold hours and dollars to get it right!
Scroll down to page 55
https://utahrails.net/pdf/EMD_567_History_and_Development_1951.pdf
Scroll down about 2 inches on the scroll bar to the crankcase stress test.
https://oldmachinepress.com/category/diesel-engines/
The mention of many inline engines out there is true. But they are not light weight aircraft engines. They have been designed strong enough to do the job, weight is not a critical issue with them. Like mentioned above the cast aluminum crankcase V12's of WW2 are very low Time Before Overhaul engines, and the more power demanded from them the less likely they are to last, unless they have been strengthened, modified.
The mention of high reving radials? The inlines are what 3000 or so?
Radials 2800 or so? We are not talking about F1 car race engines. |
|
Back to top |
|
 |
dpennings
Joined: 10 Dec 2016 Posts: 48
|
Posted: Fri Dec 11, 2020 08:26 Post subject: |
|
|
First of all, thank you for the interesting link to the EMD development! The crank case design on page 55 is quite interesting, since it is a lightweight welded design out of steel sheets. This type of manufacturing was once popular, since no complex casting was needed and weight savings could be made. I guess due to improved casting technics with reduces wall thickness and CGI with higher strength than the old gray iron, it felt out of favor.
The opposed piston engines are a world of its own, this is in no way comparable to normal engines.
Tractor pulling is no real reference; they boost every engine until it is close to collapse and destroy all kinds of big engines. If Inline engines (outside of the aircraft world, we would call most of them V-engines…) would be to week for that application, they wouldn’t use them. You should keep in mind, that Diesel engines have much higher cylinder pressures (typical 180 bar in cars, more than 220 bar in trucks) and are almost exclusively built as inline engines (except the historic Packard aero Diesel and the Nothberg stationary Diesels). I can confirm you that crankcases are not the critical point in the development process; the cylinder head is much more demanding.
The combined stiffness of an inline engine with a tight assembly out of crankcase, cylinder head & oil pan is much higher than the stiffness of an isolated cylinder in a radial engine. Of course, the designers will always try to save weight and so the crank cases are built as light as possible and only as strong as necessary. Unlike cylinder heads, which are much more demanding, since more material will not always be helpful, it is always possible to add as much strength to the crank case when it is needed. You might know, that BMW once used production inline four cylinder engine crank cases in Formula One cars and boosted them up to 800 PS (more than 1500 PS for qualification).
Meanwhile Continental offers Diesel Aero engines in inline (and “inline V”) configuration with aluminum crank cases, they are relatively short lived (TBR 1800 h), but I’m shure that’s because of the high wear rates due to high rpm and not because of cracking crank cases. |
|
Back to top |
|
 |
rwahlgren
Joined: 15 Aug 2003 Posts: 323
|
Posted: Fri Dec 11, 2020 14:12 Post subject: |
|
|
A fabricated crankcase is by no means LIGHT WEIGHT, and that process is still being used today, I think most of the OP Fairbanks Morse engines are still fabricated (welded construction) as well as the very large ship and stationary power house engines. Fabricated crankcases may be more costly ( don't know), but they never have casting flaws and can be fixed very easy when the internal parts decide to exit through the side leaving huge holes in the crankcase.
" I can confirm you that crankcases are not the critical point in the development process; the cylinder head is much more demanding. "
For the old aircraft engines they where.
Check out Kim's Chrysler Aircraft Engines book.
Need some reprints of them I just checked $300. on Amazon |
|
Back to top |
|
 |
dpennings
Joined: 10 Dec 2016 Posts: 48
|
Posted: Fri Dec 11, 2020 16:24 Post subject: |
|
|
Well according to my knowledge, welded crank cases where indeed lightweight and promoted that way (Paxman Diesel for example):
” The advantage of welded steel frame construction was a major reduction in engine weight combined with great strength. The weight of the framework itself was less than half that of the equivalent cast-iron through bolt construction used in Paxman's standard Heavy Duty Diesel Engine. The lighter weight and robustness of the steel framed version were important considerations for portable and semi-portable applications.”
[https://www.paxmanhistory.org.uk/pax-hdde.htm]
Extremely large two stroke Diesel engines like the Sulzer RTA are still welded, but the rest is all cast (MAN; MaK, now Caterpillar etc.).
I like opposed piston engines, but they are in an extremely small niche marked and the design of Fairbanks Morse hasn’t changed a lot in the past 80 years, this has little to do with the design of common four stroke engines.
The main issue with inline aluminum crank cases is the different heat expansion of steel and aluminum, this is something of which crank cases of air cooled radial engines are less affected, because the main bearings are not split and the steel cylinders are not integrated into the aluminum crank case. The differences in thermal expansion can disturb the liner roundness, the bearing clearance, the bolt tension and so on. The stiffness in terms of bending (I guess we talking about that, because you mentioned the length) is not critical, despite for acoustic behavior. A V12 inline engine offers a lot of stiffness when two six cylinder heads are being used.
Generally, in an aircraft engine you try to build everything as light as possible, so every part should be close to being critical. |
|
Back to top |
|
 |
rwahlgren
Joined: 15 Aug 2003 Posts: 323
|
Posted: Sat Dec 12, 2020 00:23 Post subject: |
|
|
"this is something of which crank cases of air cooled radial engines are less affected, because the main bearings are not split "
You may want to check out the R-4360, the only way you will get the main bearings on to that 4 throw crankshaft is for them to be split. |
|
Back to top |
|
 |
dpennings
Joined: 10 Dec 2016 Posts: 48
|
Posted: Sat Dec 12, 2020 02:48 Post subject: |
|
|
the crank case is split normal to the crank shaft, but not the bearing structure. There are steel inlays mounted inside the aluminum crank case for the main bearings, this is a very solid design without bearing deformation by screws and with minor heat expansion. |
|
Back to top |
|
 |
rwahlgren
Joined: 15 Aug 2003 Posts: 323
|
Posted: Sat Dec 12, 2020 13:41 Post subject: |
|
|
At least 2 of us keep this site going.
Yeah but you originally said this.
"this is something of which crank cases of air cooled radial engines are less affected, because the main bearings are not split "
They are split in the R-4360 and I think in R-2800.
There are no splits in the crankcase, the bearing supports fit into bores in the crankcase sections, the sections are solid forgings that are machined. The bearings are 2 piece just like your average car or truck engine.
See the sections of crankcase.
http://www.enginehistory.org/Piston/P&W/R-4360/Image86.jpg
Crankshaft etc.
http://www.enginehistory.org/Piston/P&W/R-4360/FordR-4360s/031.jpg |
|
Back to top |
|
 |
dpennings
Joined: 10 Dec 2016 Posts: 48
|
Posted: Sat Dec 12, 2020 14:46 Post subject: |
|
|
OK, I thought the crank shaft would be divided. At least, the bearing structure is made of steel and will keep thermal expansion away from the bearings.
Don't get me wrong, I like a lot of Amercan engines, but I don't understand why they never (or did they?) used the Hirth joint (https://en.wikipedia.org/wiki/Hirth_joint) which enables divided crank shafts with almost the same strength like solid ones. With Hith joints, you can avoid parting the main bearings and connection rods, it was very popular in German Race and flight engines (also used in Japanese racing Motorcycles).
We need to keep this forum alive! |
|
Back to top |
|
 |
kmccutcheon

Joined: 13 Jul 2003 Posts: 298 Location: Huntsville, Alabama USA
|
Posted: Sat Dec 12, 2020 16:40 Post subject: |
|
|
dpennings wrote: | Don't get me wrong, I like a lot of Amercan engines, but I don't understand why they never (or did they?) used the Hirth joint. |
Pratt & Whitney "C" and later R-2800 engines used Gleason face-spline joints, which were superior to Hirth jointsr. P&W tested the Hirth joint, but found it lacking.
Wright used clamp crankshaft joints, which appear to have been adequate for the application. _________________ Kimble D. McCutcheon |
|
Back to top |
|
 |
dpennings
Joined: 10 Dec 2016 Posts: 48
|
Posted: Mon Dec 14, 2020 07:20 Post subject: |
|
|
Now it came back into my mind, that I've seen it on a Pratt and Wittney (in the Chanel of Kermit Weeks).
On the first glance, this looks the same like the Hirth connection, do you know the difference between them? |
|
Back to top |
|
 |
kmccutcheon

Joined: 13 Jul 2003 Posts: 298 Location: Huntsville, Alabama USA
|
|
Back to top |
|
 |
dpennings
Joined: 10 Dec 2016 Posts: 48
|
Posted: Mon Dec 14, 2020 14:17 Post subject: |
|
|
thanks, but I still don't see the difference between the Hirth joint an the Gleason type, maybe some angles are different or other minor geometries, but the principle is the same.
The Dusevoir Paten shows something completly different to me, maybe I just couldn't open more pages? |
|
Back to top |
|
 |
|
|
You cannot post new topics in this forum You cannot reply to topics in this forum You cannot edit your posts in this forum You cannot delete your posts in this forum You cannot vote in polls in this forum
|
Powered by phpBB © 2001, 2005 phpBB Group
|