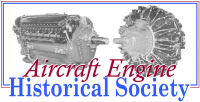 |
enginehistory.org Aircraft Engine Historical Society Members' Bulletin Board
|
View previous topic :: View next topic |
Author |
Message |
jjuutinen
Joined: 13 Jul 2003 Posts: 180
|
Posted: Thu Oct 18, 2007 18:18 Post subject: Crankshaft experts ahoy! |
|
|
WW Two tank engines by Maybach firmk had peculiar crankshaft design. Crankwebs were circular and of large diameter and it ran on large roller bearings. The circular crankwebs had the roller path machined on them. In some sources this is called a "disc crankshaft". One British report mentions the design allowed short crankshaft. Any idea what are the other pros and cons of this design? |
|
Back to top |
|
 |
gwhite
Joined: 13 Jul 2003 Posts: 58
|
Posted: Fri Oct 19, 2007 13:27 Post subject: |
|
|
This design allows for a one piece c/case. Offy used this design concept for their Indy 500 engines.
Not sure that I understand how it makes the engine/crankshaft shorter, the lenght is determined by the bore and cylinder spacing. |
|
Back to top |
|
 |
jjuutinen
Joined: 13 Jul 2003 Posts: 180
|
Posted: Fri Oct 19, 2007 18:43 Post subject: |
|
|
I believe (based on looking at the drawings of the crankshaft) the shortness is due to the very narrow bearings it had. And, that is what the report by British Tank experts stated! |
|
Back to top |
|
 |
klankenau
Joined: 15 Nov 2005 Posts: 45 Location: Dallas, Texas
|
Posted: Wed Oct 24, 2007 11:02 Post subject: |
|
|
Roller and ball bearing cranks are not ununusual. One very common example is the Austin 7 (747cc) sidevalve engine. Hundreds of thousands were produced with little change from the mid-twenties up until the 1970's (later and larger engines built by Reliant).
Many motorcycle and WWI rotary engines also use roller & ball bearing cranks. |
|
Back to top |
|
 |
jjuutinen
Joined: 13 Jul 2003 Posts: 180
|
Posted: Wed Oct 24, 2007 12:47 Post subject: |
|
|
True. But in this case the specialty is the very large diameter of the bearings. If you put this crankshaft on a table, it would roll off on the bearing races at the mildest inclination. It is a crankshaft type I have NEVER seen in any other maker´s engines and is pretty much unknown in standard engine design textbooks. |
|
Back to top |
|
 |
cmalott
Joined: 20 Dec 2005 Posts: 8
|
Posted: Thu Oct 25, 2007 02:04 Post subject: Roller Cranks |
|
|
I might be missing something here, but one reason ball and roller bearing cranks are made up of pressed-together discs and pins is that's the only easy easy way to get it together. On most of the smaller engines the rod bearing rollers are held in a round unbroken retainer. Some of the lower speed stuff used no retainer, with the rollers against each other, They used a one piece crank with rods having split big ends.
Cork |
|
Back to top |
|
 |
jjuutinen
Joined: 13 Jul 2003 Posts: 180
|
Posted: Thu Oct 25, 2007 06:23 Post subject: |
|
|
Would it help if I could link to a picture of the crankshaft? For me it hepled a great deal. |
|
Back to top |
|
 |
cmalott
Joined: 20 Dec 2005 Posts: 8
|
Posted: Thu Oct 25, 2007 10:11 Post subject: pressed up and o/w fab'd cranks |
|
|
It would help at lot to post the link. Cork |
|
Back to top |
|
 |
pshort
Joined: 13 Jul 2003 Posts: 50 Location: Auckland, New Zealand
|
Posted: Mon Oct 29, 2007 00:36 Post subject: |
|
|
I agree the Maybach heavy-duty petrol V-12 engines have an unusual main bearing design. It is nothing like the crank designs mentioned in other posts.
There are drawings of these engines (cross-section side and end views) in “Karl Maybach His Engines and Automobiles” by Harry Niemann. There are main bearings either side of every crank pin. What is unusual (for those who haven’t seen the book) is that the “webs” for the crank pins have become full discs, and it is these discs that have become the main bearing inner races. The main bearing journal diameter is huge. There is a thin outer race on these bearings, flanged to hold the rollers. The shortness of the crankshaft comes not through reduced bearing lengths, but by utilising almost the entire crankshaft length as either big-end or main bearing journal.
Apparently the first of these unusual crankshafts for heavy duty petrol V12’s appeared in 1935 in the HL 100 TR, 10.8 litre engine. They were called a Scheibenwelle (disc shaft) and are described by historian Kurt Schnauffer like this:
”To keep the engine as compact as possible, and still have space for the connecting-rod bearings, Maybach utilised discs as main bearings, rotating in the engine block. Naturally this crankshaft was very short and therefore extremely resistant to rotary vibration. The crank itself had roller bearings, and the connecting-rods had plain bearings.”
Apparently most or all German tanks were fitted with Maybach engines; they were made in the tens of thousands. The capacity and power output greatly increased during the war, but apparently the engine length didn’t increase, no doubt this design allowed for the closest possible spacing of cylinders.
The tunnel crankcase was not new. I don’t know who used it first, but notable early users were Peugeot in their famous 1913 GP engines, Ballot, Miller, Offenhauser also post WW2 Lagonda 2.6 litre and Armstrong Siddeley 3 litre. However, all these engines used “conventional” mains, whether plain, roller or ball, in that they were placed between the crankpin webs. Also, all these engines used a diaphragm, whether split or one piece, to take up the space between the main bearing and the tunnel diameter in the crankcase. The Maybach, because of its very large diameter mains was able to use the outer race of the bearing directly in the crankcase tunnel.
The highest rotation speed I can find listed for the various Maybach V12s’ is 3000 rpm.
Karl Ludvigsen in his excellent book ”The V12 Engine” describes a Mercedes-Benz automotive V12 (M148) designed around 1938 as an answer to Maybach and other luxury automotive competitors. This engine had four mains, all plain bearings, but the middle pair were of similar type to the Maybach described above. The main bearing journals and adjacent crankpin webs became one - huge journals of 160mm diameter running on white metal bearings in a tunnel crankcase. The two end mains were of more conventional size and so used diaphragms to take up the distance between journal and tunnel. All four mains were water cooled.
Karl mentions that Maybach and Tatra both used this design (but with balls or roller mains) and that possibly Hanomag used the design in a truck engine.
The advantages mentioned for the MB design are the shortness (and consequent stiffness) of the crankshaft and the almost-equal close spacing of the cylinder centres. Apparently only a handful of V12 cars were built, the engines could rev to 3,800 rpm. However war-time demand meant that 3,420 were built in de-rated and modified form as engines for stationary use, e.g. driving generators for search lights.
I came across mention of a working Maybach petrol V12 a while back, it powers a Tiger tank restored at the Bovington Tank Museum. They initially managed to ruin one engine with a conrod exiting the block, but sounds like they have replaced it and have it running again.
After writing all the above I found this page showing a crankshaft and drawings of a HL 210 engine. It differs slightly from the drawing of the HL 120 engine mentioned in the Maybach book (eg conrods changed from side-by-side to forked type, plus engine size greatly increased):
http://www.alanhamby.com/maybach.html
Display using original engine HL210: http://www.tiger-tank.com/secure/journal41.htm
Some engine components: http://www.tiger-tank.com/secure/journal28.htm
Shows how close the cylinder bores are (though sleeves not fitted): http://www.tiger-tank.com/secure/journal34.htm
Last edited by pshort on Mon Oct 29, 2007 03:56; edited 1 time in total |
|
Back to top |
|
 |
jjuutinen
Joined: 13 Jul 2003 Posts: 180
|
Posted: Mon Oct 29, 2007 02:16 Post subject: |
|
|
Thanks for posting thise images as it saved me a lot of troubles! BTW, the engine used in the Tiger had very poor torque rise characteristics, only some 10% while best tank engines had 20-35% torque rise (e.g. GM diesel, Soviet V-2 diesel, Ford GAA, Chrysler A-57). According to a German report, a combination of zero torque rise engine and an 8-speed gearbox has the same "driveability" than a combination of 33% rise and 5-speed box. This displays how significant the torque rise is. |
|
Back to top |
|
 |
wallan
Joined: 13 Jul 2003 Posts: 252 Location: UK
|
Posted: Mon Oct 29, 2007 06:17 Post subject: |
|
|
Another few reasons for using a barrel crankcase, is that there is no horizontal split creating a seperate sump, which strengthens the crankcase, and gives one less area that can leak oil. The front of the crankcase only needs a smaller hole for the end of the crankshaft to stick through. A major reason for choosing this design is that the crankshaft can be withdrawn from the engine without having to remove it from the vehicle. |
|
Back to top |
|
 |
pshort
Joined: 13 Jul 2003 Posts: 50 Location: Auckland, New Zealand
|
Posted: Mon Oct 29, 2007 15:53 Post subject: |
|
|
wallan,
Can you think of any case of a barrel-type construction in which one might want to withdraw a crankshaft with the engine in place? It sounds highly unlikely to me. Imagine even trying to physically do this. Apart from the fact that it would just be bad practise, engines like the Lagonda 2.6 had the crankshaft inserted from the rear (front main was a bush), and other common engines like the Offy required a heated crankcase besides which I am sure no good mechanic would fool around with the engine in the car.
I have read how it is easier to seal the bottom end of the engine with this construction, (I agree for the main seals), but you still need to remove the con rods before the crankshaft can be removed, hence these engines either had removable sumps or plates for access. Also, it is possible that the early Maybach engines did have a split barrel construction - the drawing in the Maybach book appears to show a horizontal part line. Further, I have worked on "conventional" engines which use one-piece oil seals on front and rear mains, they seem to offer every advantage the barrel-type boast of (as far as oil tightness goes).
Engines like the Lagonda used cast iron crankcase and aluminium diaphragms, there was clearance between the diaphragm and barrel, plus each diaphragm was slightly different in size to ease installation. What a nightmare. I knew a guy who worked on Lagonda and Jaguar engines (both appeared in the same year, 1948). He hated those Lagonda crankcases - a "great" idea from some guy on a drawing board (well, W.O. Bentley actually), but a pig to repair and unnecessary as proven by the majority of manufacturers who avoided it. When Aston Martin later took over this engine they ditched the barrel idea and fitted conventional caps. (Admittedly this was combined with change to aluminium crankcase which is harder to make work in the barrel design).
The barrel-type racing engines (as far as I can read) required the whole crankcase heated to insert the crank/diaphragm assembly. I guess this is because they often used aluminium crankcases, so required the diaphragms to be a press fit. I think the diaphragms were often bronze. (In a cast iron crankcase, the aluminium diaphragms can be fitted without press fit, but will expand and tighten when hot. In theory that is, but one book I have says the Lagonda bearings were not tight enough).
Fortunately Offenhauser developed a cruciform-shaped split diaphragm with cut-outs in the crankcase, so the whole assembly could be "easily" dropped almost into place, then the cruciforms turned slightly and the final engagment of the diaphragms into their seats and onto their studs takes place. For a while the crankcase notches were deleted and it took several more difficult hours to do the same job (Diaphragms had to fitted in halves, after the crank was in the crankcase). |
|
Back to top |
|
 |
|
|
You cannot post new topics in this forum You cannot reply to topics in this forum You cannot edit your posts in this forum You cannot delete your posts in this forum You cannot vote in polls in this forum
|
Powered by phpBB © 2001, 2005 phpBB Group
|