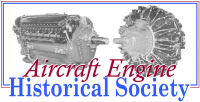 |
enginehistory.org Aircraft Engine Historical Society Members' Bulletin Board
|
View previous topic :: View next topic |
Author |
Message |
szielinski

Joined: 13 Jul 2003 Posts: 94 Location: Canberra, Australia
|
Posted: Thu Feb 01, 2007 18:21 Post subject: Slding gearing for gearheads... |
|
|
Just blowing the dust off my old sleeve valve engine idea after reading the g4g articles in TM. I couldn't see anything about sliding friction/loads ALONG the gear's axis.
So my question is this, if you have a set of straight-cut gears, and they constantly slide over each other axially, is there any weird or excessive tooth loading? _________________ “Make everything as simple as possible - but not simpler” – Einstein. |
|
Back to top |
|
 |
hholzer
Joined: 13 Jul 2003 Posts: 4
|
Posted: Fri Feb 02, 2007 23:03 Post subject: Gear driven Sleeve Valves with lateral gear sliding action |
|
|
Greetings Fellow Sleeve Valve Nut!
I dont see any "funny" tooth loading or deflection when driving rotation of an integral Gear Sleeve with a possibly reciprocating Rack or oscillating drive gear (provided that the drive gear is not too small). Presumably the Sleeve's rotation (preferably oscillating rotation) will cause Sleeve axial displacement by virtue of cam action between something like a radially extending contoured "fin" on the sleeve against something like an axially separated pair of rollers fixed to the "block" or crankcase.
LUBRICATION with the extra lateral rubbing of the Gear faces may well be a problem. A generous relief contour in the "upper"and "lower" lateral edge regions of the Drive Gear faces should aid the establishment of hydrodynamic oil film lubrication against the axial (lateral) slide or "rubbing" action. This COULD also help with lubrication of the normal gear action provided that there is an ample lubricant delivery to the area.
I hope that this scheme is built and fairly tested and developed. And while you are at it, how about incorporating another Evil Scheme that I have dreamed about for decade or so?
Modern competition engines strive for more valve area. The sleeve valve engine as normally presented doesn't have an area advantage over the poppet valve type. BUT suppose for a moment that we run 4-stroke with sleeve valve exhaust occupying all possible sleeve valve space in the upper cylinder and then add a full complement (1,2,3,4?) of poppet intake valves to the "Junk Head"? We've just nearly doubled the valve area!
Or, as Kevin Cameron reminded me once, the hot exhaust valve is sort of needed in today's Grand-Prix engines to incite sufficiently rapid burning at high revs. The same may well be true of Diesels. In those cases let's use Poppet Exhaust Valves in the "Junk Head" and swirl inducing Sleeve Valve peripheral intake (cylinder) ports.
Are you aware of Mike Hewland's Sleeve Valve work? I have a copy of a magazine article and some correspondence on he topic which may be of interest. I will send copies to Kimble McCutcheon so that he may forward them.
Good Fortune with your project! Phil Miller |
|
Back to top |
|
 |
szielinski

Joined: 13 Jul 2003 Posts: 94 Location: Canberra, Australia
|
Posted: Sun Feb 04, 2007 16:46 Post subject: |
|
|
"will cause Sleeve axial displacement by virtue of cam action between something like a radially extending contoured "fin" on the sleeve against something like an axially separated pair of rollers fixed to the "block" or crankcase. "
Interesting case of "six of one, half a dozen of another" in engineering. That is, you came up with a similar idea for sleeve motion but via a different route.
Following on from that, what about a narrow driven gear with a wide driving gear?
(Something like driven gear width = 1/5->1/3 sleeve travel)
With a taper on the driven teeth, would that put undue twist on said teeth? Would it be worth (or even possible) drilling holes in the drive gear to improve hydrodynamic lubrication?
(yes, yes, more oil mist to condense back to the oil pump...) _________________ “Make everything as simple as possible - but not simpler” – Einstein. |
|
Back to top |
|
 |
hholzer
Joined: 13 Jul 2003 Posts: 4
|
Posted: Sun Feb 04, 2007 22:04 Post subject: Narrow driven gear/wide drive gear sleve valve drive |
|
|
I can think of no basic reason as to why a narrow driven gear/wide drive gear combo could not be equally satisfactory. BUT longer teeth on the necessarily relatively thin sleeve may be an easier path to the strength needed in this area. On the other hand this arrangement may require a longer sleeve extension into the crankcase than is practical.
It follows that a narrow driven gear/wide toothed driving rack which would spread the driven gear loading better through the improved contact ratio of this combo may be the best compromise choice.
The potential lubrication problem of the lateral sliding gear or gear & rack arrangement is, to me at this point, of uncertain severity. I habitually first expect the worst and then try to think of ways around problems before they actually appear. This used to be referred to as the "WHAT IF?" procedure. You know: "WHAT IF the main shaft breaks? Does the Turbine then overspeed and disintegrate and saw the airframe in half?" And a good first answer is: "Not if the thrust bearing is arranged so as to now allow the turbine wheel to blow back into the next aft stator and grind to a halt before it centrifuges apart."
So it is with the lubrication concern. I imagine what amounts to a lateral edge chamfer on the "upper" and "lower" edges of the shorter width gear, be it driver or driven. I hope that this will help defeat the potential lube problem that excited my "WHAT IF" thoughts. I hope that a "chamfer" requirement will not grow into large "tapers" that would substantially reduce the strength of the shorter face gear teeth.
In any case gear strength calculations are possible with conservatively assumed sleeve inertia, accelerations, and friction values and this should lead to satisfactory gear choices and design probably based only on the UNCHAMFERED PORTION OF THE SHORT FACE WIDTH GEAR.
You are right. Oil mist in the crankcase can be a problem BUT it is also very good for rolling element bearings and high speed gearing though it will not likely prove necessary for your sleeve gear drive scheme. There may well be sufficient oil flying about in the crankcase to serve the sleeve drive well with no special attention at all. BUT jets delivering oil to the "chamfered" face edges of the shorter face gears as they enter mesh (from either side if the sleeves are oscillating) is my first offer as an answer to the "WHAT IF?" question in this area.
Oil holes in drive gears could be useful and are certainly an elegant thought. I don't know yet if they will be necessary and there are also seemingly simpler potential solutions that could be tried first.
Please keep gnawing on your gear driven sleeve valve idea in thought and start, if you haven't already, contemplation of an elementary test rig.
Keep up the Good Work! Phil Miller |
|
Back to top |
|
 |
|
|
You cannot post new topics in this forum You cannot reply to topics in this forum You cannot edit your posts in this forum You cannot delete your posts in this forum You cannot vote in polls in this forum
|
Powered by phpBB © 2001, 2005 phpBB Group
|